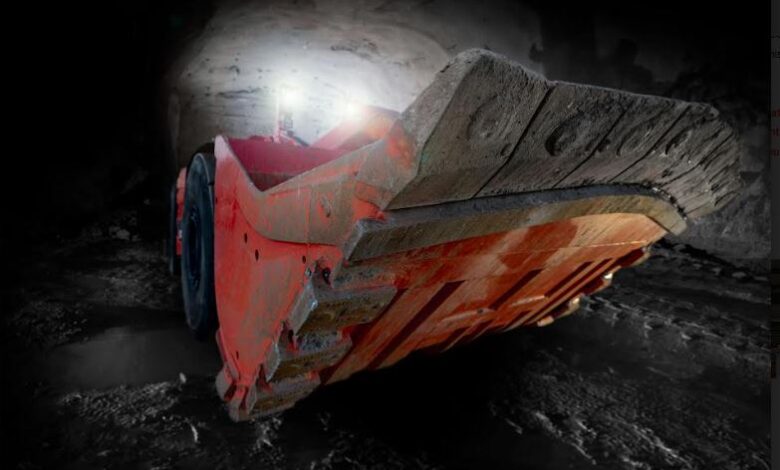
Avoiding load losses by keeping buckets in good shape
With mining’s highly abrasive conditions, it is no wonder that loader buckets wear quickly; but Sandvik has the solution to extend bucket life and maintain high productivity.
The company’s Shark™ range of ground engaging tools (GET) has been evolved over two decades, delivering longer bucket life while cutting the cost of ownership by almost half over the total life of the bucket. In South Africa for the Electra Mining Africa show in September 2022 was Darren Scott, Sandvik’s GET business development manager for south-east Asia and Africa. Scott highlights that Shark™ GET enhances the structural strength of buckets to allow more tonnes to be shifted.
“A worn bucket is highly inefficient for the whole mining operation,” he argues. “When the leading edge wears, there is reduced penetration into the muck pile, as well has higher fuel usage as the machine has to work harder.”
Another result is more wear and tear on consumables like tyres, which must exert greater force and may even spin as the machine tries to penetrate the material it is loading. The real casualty, though, is productivity; the volume of material moved can drop by 20% per cycle when a bucket is severely worn.
Worn buckets
“In a mine that operates a number of LHDs, we estimated that worn buckets were costing the operation over 50,000 tonnes a year in lost production,” he explains. “By installing Shark™ GET the drop in loading capacity was limited to 5%, saving almost 40,000 tonnes; this translated into over US$10 million in revenue that the customer could add to their income in a year.”
Among the options in the Shark™ GET offering is the Blue Pointer™ 2 range which provides ease of mechanical attachment, while the Half Arrow range offers the simplicity and strength of a weld-on solution. Under the Shark™ brand, Sandvik also markets weld-on and mechanical heel shrouds, as well as plate profile bars and cast profile bars. With Sandvik’s centre of excellence for GET&B in Australia, the brand’s success is also thanks to the specialised hard-wearing metallurgy that the company has developed in-house.
“The different versions of our Blue Pointer™ 2 lip protection systems, for instance, are constructed with our wear resistant Sandvik SS3000 or SS5000 steel alloy,” says Scott. “We use our Sandvik SS2000 alloy in our Half Arrow series, and our weld-on heel shrouds.”
As an indication of how popular the Shark™ brand has become, he explains that it is not only applied to Sandvik loaders but is extensively used on competitor machines.