Scope for private steam turbines to feed grid, says WEG Africa
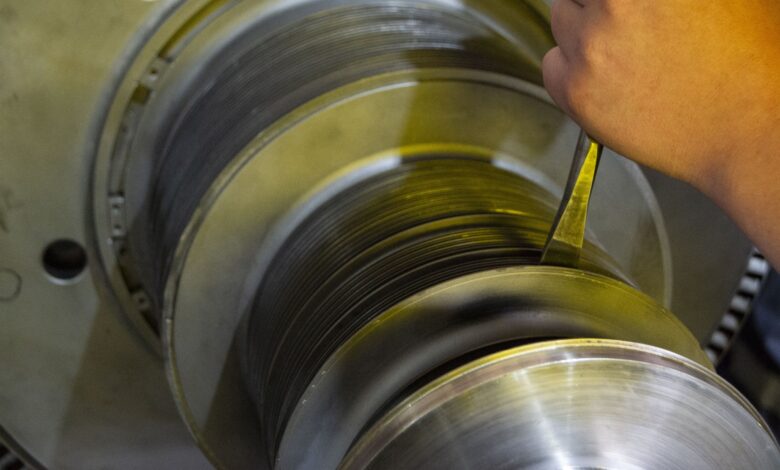
Steam turbines represent mission critical equipment for a range of industries from sugar and paper to steel and petrochemicals, but there is now greater opportunity among these sectors to generate more energy to sell into the national grid.
Traditionally, companies using steam turbines have usually consumed all the energy they produce in their processes – with a range of benefits such as supply reliability and cost savings. As the country struggles to keep up with power demand, however, there are more opportunities for the private sector to produce excess electricity for sale into the grid.
According to Alastair Gerrard, Executive Energy Systems at WEG Africa, this trend is already advanced in Brazil – the home of holding company WEG. Many steam turbine users in Brazil have capitalised on these opportunities by increasing their boiler efficiency.
“While it may be common in South Africa’s sugar industry, for example, to use medium pressure boilers, the Brazilian market uses high pressure boilers up to 140 bar – and gain significant efficiencies with these higher pressures,” says Gerrard. “This allows these sugar producers and other users to upgrade their facilities and considerably augment their revenues through the sale of electricity, while also paying off their capital investments much quicker.”
Economic growth
He points to the government’s strategic direction in establishing the National Transmission Company of South Africa, a key step in transforming the country’s electricity industry. This will open doors for more private companies to ‘export’ excess electricity into the grid, helping to stabilise supply and strengthen the foundation for economic growth.
“This has been successfully achieved in countries like Brazil, and it is exciting to see that we are making progress on this journey in South Africa,” he says. “We believe that WEG Africa has an important role to play in this endeavour – through our long experience in this field and our full service offering for steam turbine users.”
Cobus van Eeden, WEG Turbine Services Manager at WEG Africa, highlights that the company offers customers a turnkey capability. It sizes steam turbine solutions according to the specific operating parameters of the customer’s application, and supplies a bespoke thermal power system. The service also includes installing the machines, commissioning and ongoing after-sales servicing and maintenance.
“As an OEM of steam turbines, gearboxes and generators, we can even help customers to assess their current equipment – whether these are WEG products or from other OEMs – and provide strategic options and recommendations,” says van Eeden. “In addition to our depth of engineering expertise for repairing such equipment, we can also analyse the potential for enhancing operational efficiency and increasing power output capability of the equipment.”
The company provides long term service level agreements, including contracts for preventative maintenance. WEG Africa also works with customers on their forward planning, which may include considering the transition to electricity exporting.
Gerrard points out that this approach is built on its commitment as an OEM to stand alongside customers throughout the lifecycle of the equipment supplied. He notes that, while there has in the past been some acceptance of third-party support in this field, WEG Africa favours in-house OEM support for its solutions through service level agreements that give customers confidence in the total lifecycle cost of their purchase.
“Our field service technicians – active in many African countries and offshore – are on site with customers, developing a thorough understanding of their equipment and requirements,” he explains. “We integrate this information within our various functions to deliver the most valuable response and guidance on maintenance scheduling.”
Van Eeden outlines WEG Africa’s extensive engineering capability which includes machine servicing on customers’ sites – from gearboxes and turbines to generators and control systems. Equipment requiring more intensive work can be transported to the company’s 1,200 m 2 workshop east of Johannesburg, which prides itself on quick turnarounds.
“Our facility includes full engineering capabilities, including the repair and manufacture of turbine bearings as well as the ability to conduct aftermarket engineering and optimising of numerous components,” he says. “We achieve this through our skilled machinists and technical staff, working with sophisticated scanning and engineering tools.”
In-house access to specialised facilities such as a labyrinth rolling machine for sealing strips, as well as a sandblasting booth for preparing components, further underpins the quality of workmanship and efficiency – thereby minimising downtime for customers.